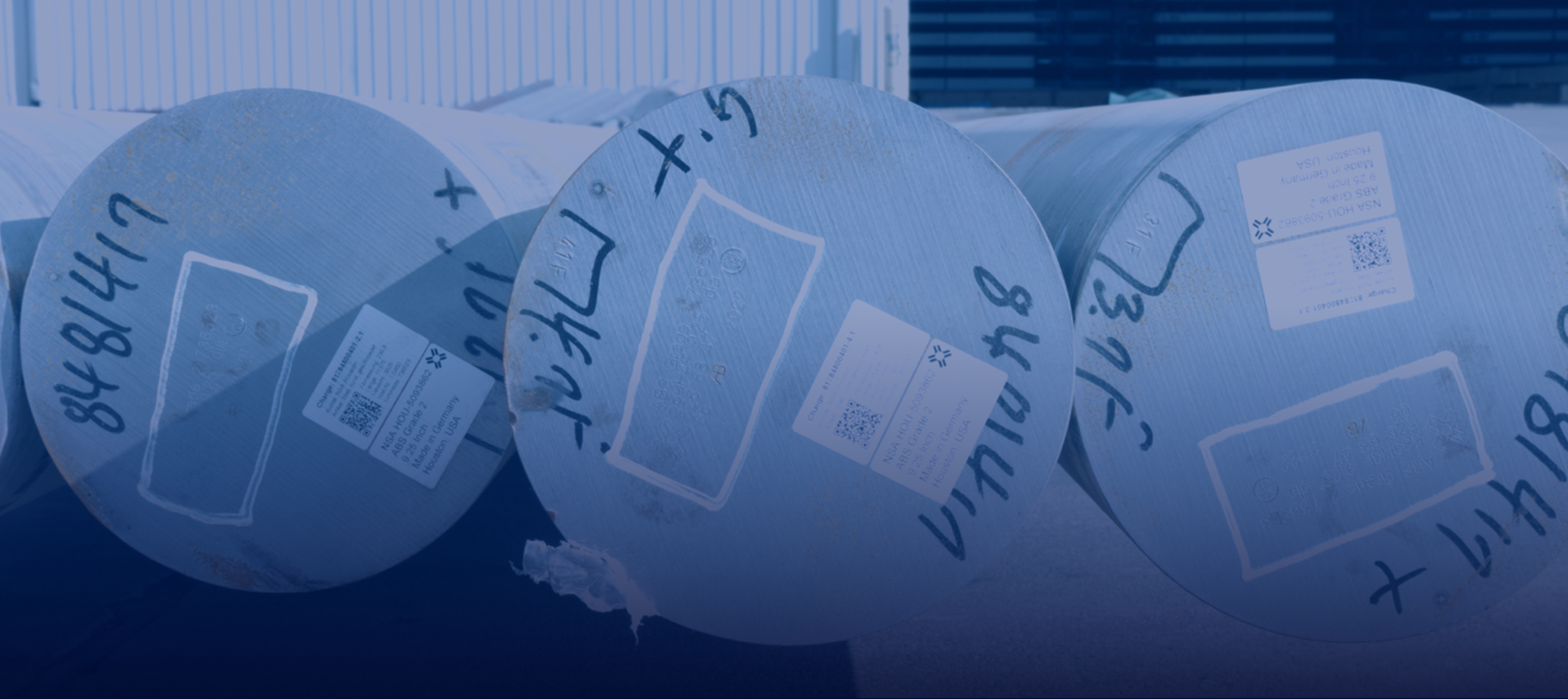
ABRASION – A process of rubbing, grinding, or wearing away by friction; a natural wear of material in the field.
AIR HARDENING STEEL – Using alloy steel capable of forming martensite (a transitional phase) to develop a high hardness through air cooling at a predetermined temperature.
ALLOY – Any metal that is a blend of more than one kind of metal.
ALLOY STEEL – A type of steel containing higher quantities of certain elements affecting the mechanical or physical properties and the overall machinability.
ANNEALING – Heating of a metal to a predetermined temperature for a suitable time and cooling at a rate to accomplish the objective.
Annealing objectives include:
a)Relieve stresses
b) Induce softness structure
c) Improve physical, electrical or magnetic properties
d) Improve machinability
e) Refine crystalline structure
f) Remove gases
ATMOSPHERE – Gaseous environment surrounding a material during heat treating. This environment can protect or alter the chemistry of material, through the addition or removal of metallic elements.
AUSTEMPERING – Process of cooling a primarily iron alloy at a fast rate froim a temperature above the transformation range, in a suitable medium. During this procedure, the material is held at that temperature until modifications of the desired intermediate structure is complete.
AUSTENITE/AUSTENITIC – Non-magnetic steel which cannot be hardened through normal heat treatment, yet can be work hardened.
AUSTENIZING TEMPERATURE – A temperature at which steel is substantially all austenite, (which includes being a solid solution of one or more elements).
BASIC STEEL – Steel produced in a furnace that is bottomed and lined with basic substances, such as a nagnesia or lime. This allows the removal of sulfur and phosphorus during the melting process.
BEARING LOAD – A load supported by a member.
BEARING STRENGTH – The maximum amount a bearing load can handle.
BILLET – A semi-finished round or square form of steel that can be hot worked through forging, rolling or extrusion. Used to make long products such as bars.
BLISTER – A dome shaped defect sometimes found on or near the surface of metal, due to a gas expansion in the subsurface zone.
BLOOM – A semi-finished form of steel, no wider that 8", which will eventually be further processed into beams, rods, bars and tubing products.
BLUING – Refers to a thin blue film of oxide that forms on a scale or rust free surface of a ferrous (or metal primarily composed of iron) alloy. Occurs when metal is subjected to a specific agent while at a particular temperature. Bluing improves the overall appearance and resistance to corrosion.
BRIGHT ANNEALING – Heating in a protective atmosphere to prevent discoloration.
BRINELL HARDNESS TEST – A test to determine the hardness of steel. This is conducted through a process of subjecting a steel/carbide ball to a specific weight load and calculating the hardness. Dividing the load applied by the surface area of the indention made by the weight gives you the brinell hardness.
BURNISHING – Term used to define the frictional contact that smooths a surface using hard "ball like" pieces.
CARBON STEEL – Also known as ordinary steel, straight carbon steel and plain carbon steel because it is the most widely produced. It is a basic combination of carbon and iron, primarily relying on the structure of the carbon element.
CENTRIFUGAL CASTING – Process of pouring metal into a mold, which rotates as the object/cast hardens. Commonly used for couplings, rings, seals, etc.
CHAMBER – Beveling an edge or surface in order to relieve the sharpness.
CHARPY TEST – Determines the impact strength of a bar. Through a testing process, where material is first notched in the center, and supported at both ends, a single blow is made to the center by a pendulum. The absorbed energy is determined by the rise of the pendulum, which measures the impact strength, or notch toughness.
COLD WORKING – Changing the structure and shape of steel by an external force to increase its hardness and toughness. The process can be executed through rolling, hammering, or stretching the material at a temperature low enough so re-structuring does not occur.
CONTINUOUS CASTING – A way of forming a material using a mold. The process includes pouring steel into a billet, bloom or slab directly from the furnace into the opening of the mold. The steel is continuously solidified as it passes through and exits the mold’s shape, until it reaches the desired length. Continuous casting is ideal for producing semi-finished mill products.
CORE – The interior part of steel whose composition has not been changed in a case hardening operation.
CORROSION EMBRITTLEMENT – A loss of ductility in a metal due to a natural degradation, usually within the grain of the material and not visible.
CORROSION FATIGUE – Damage or failure of a metal due to corrosion combined with repeated or fluctuating stresses.
CRITICAL COOLING RATE – Minimum cooling rate that will suppress undesired transformations in a metal.
CRITICAL POINT – Point at which a change will start or be complete in the crystal structure, phase or physical properties of a material due to incurring temperature or pressure.
CRITICAL RANGE – A temperature range for the reversible change between an upper and lower critical point for a specific material.
CUTTING SPEED – The rate metal moves past the edge of a tool used to remove stock. Basically the difference between the cutting tool and the surface of the workpiece.
DRAW – Term used to refer to the process of pulling/drawing a material out of a die, sizing it or increasing the physical properties. This term is also used interchangeably with tempering.
DROP FORGING – Forming a material into a fixed shape using a falling weight, such as a drop hammer.
DUCTILITY – The ability of steel to be formed, shaped or altered permanently at room temperature without being damaged.
EDDY-CURRENT TESTING – A form of nondestructive testing in which an "Eddy Current Flow" is induced into the test object. Changes in the flow are reflected into nearby coil or coils for analysis indicating certain properties or defects in the material.
ELASTIC LIMIT – The maximum amount of stress a material can handle without permanent strain after the stress is released.
ELONGATION – Term used in tensile testing, which is the difference between guage lengths of an object’s original state versus its state after fracture due to extension. The elongation is usually expressed as a percentage.
FATIGUE LIMIT – Defines the maximum amount of stress a particular material can endure without failure for an infinite number of cycles.
FATIGUE STRENGTH – The maximum amount of repeated stress a material can withstand for a specific number of cycles before failure occurs.
FLAME ANNEALING – The careful heating of a metal part by flames before or after working.
FLAME HARDENING – A surface hardening process involving a localized flame, which heats the material above the austenite transformation temperature and is later followed by quenching to produce a desired hardness.
FORGING – The working of hot or cold metal to a predetermined shape through hammering upsetting, pressing, rolling or a combination of these processes.
FRACTOGRAPHY – The study of microscopic fractures in metal surfaces through the analysis of photographs taken of the actual "fracture surfaces".
FRACTURE TEST – A test carried out by nicking or breaking a bar, by means of sudden impact, in order to examine the fractured surface with the naked eye or even a low powered microscope. This test is used to determine basic information such as composition, grain size, case depth, soundness and presence of defects.
FREE MACHINING – Term used to describe steels that have been infused with specific quantities of elements enabling them to machine more easily than untreated grades. Some characteristics include production of small broken chips, lower power consumption, better surface finish and longer tool life.
FULL ANNEALING – A general term used to describe the heat treating cycle that produces a material’s minimum strength and hardness. Process is carried out through heating the material above its critical temperature and allowing it to cool slowly throughout the transformation range.
GALLING – Term used to describe the condition that develops between high spots due to excessive friction. This condition can result in localized welding or oppositely chipping the material.
GRAIN SIZE – In metals, this is a measurement of the area or volume of grains in a polycrystalline material. Grain size has an important effect on the physical properties of materials. Generally, fine grain steels have a better combination of strength and toughness whereas course grain steels have better machinability.
GRANULAR FRACTURE – A type of irregular surface produced where material is broken or cracked along the grain structure. Characterized by a rough grain like appearance as opposed to a smooth one.
GRINDING CRACKS – Shallow surface cracks usually appearing on relatively hard materials as a result of incorrect grinding, caused by the generation of high heat and rapid cooling on the area of contact.
GUNDRILL – A type of drill used for deep hole drilling, usually having multiple flutes and coolant passages through the drill body enabling drill holes up to 120" long.
HARD CHROMIUM – Term usued to describe chromium that is deposited specifically for engineering needs rather than decorative applications. This element can be deposited by electrolysis (a chemical change by an electric currect) on a corrodible metal, which can increase the overall wear resistance.
HARDENING – Process of increasing the hardness of a material through a suitable treatment usually involving heating and cooling.
HONING – Process less intense than grinding used to remove thin layers of stock. Producing uniform high dimensional accuracy and fine finish, typically used on the inside of cylindrical surfaces.
IMPACT TEST – A test that determines the potential behavior of materials when they are subjected to different stresses. These can include high rates of loading, bending, tension and torsion. Similar to a Charpy Test, the quantity measured is the resulting amount of energy absorbed after breaking the test piece by a single blow.
INCLUSIONS – Particles of foreign material (or impurities) that are nonmetallic, which separate from the liquid steel and are mechanically held in during solidification. The impurities may be simple or complex oxides, sulfides and silicates. Generally, inclusions are detrimental to the material’s mechanical properties, but in some grades they are made intentionally to improve machinability. Inclusions can be detected through Ultrasonic Testing (UT testing).
INDUCTION HARDENING – Localized heating of the surface area through alternating electric currents which heat the material above the critical temperature and immediately submit it to the quenching process.
INTERRUPTED QUENCH – Stopping the cooling cycle at a predetermined temperature and holding at this temperature for a specific time before cooling to room temperature. Usually done to minimize the likelihood of cracking, or to produce a particular structure in the part.
INVESTMENT CASTING – Process of pouring molten metal into a specific type of mold which expands and surrounds the material. The mold later sets at room temperature and can finally be removed from the finished cast through the use of heat.
LAMINATIONS – Metal defects generally aligned parallel to the worked surface of the material; resulting from blisters, seams, inclusions, etc.
LAP – A surface imperfection with the appearance of a seam, usually caused by hot metal fins or sharp corners being folded over and rolled or forged into the surfaces, without being welded.
MACHINABILITY – Measure of ease at which a metal can be machined satisfactorily.
MACROSTRUCTURE – The structure of metals which can be seen through macroscopic examination of the etched surface of a polished specimen. The macroscopic examination includes the magnification up to ten diameters.
MAGNETIC PARTICLE INSPECTION – A nondestructive method of detecting cracks or defects by establishing a magnetic field in the object and using iron fillings to see if the field lines are constant.
MARTEMPERING OR MARQUENCHING – A form of interrupted quenching where steel is quenched rapidly until the temperature is uniform, then air cooled to room temperature. Hardening of the material occurs when the air cooling begins. Martempering is ideal for low to medium alloy steels where distortion may be a problem.
MARTENSITE – A hard transformation product, technically considered a supersaturated solution of carbon in iron. This is characterized by an acicular (or needle-like) pattern in the microstructure in both ferrous and nonferrous alloys. Martensite can be transformed into austenite when steel is quenched and cooled below 450 degrees F resulting in a hardness varying from 30 to 68 Rockwell, depending on the carbon content.
MECHANICAL PROPERTIES – Material characteristics in response to externally applied forces. These forces indicate the material’s suitability for mechanical applications. For example, modulus of elasticity, tensile strength, yield strength, elongation, hardness and fatigue limit.
MICRO STRUCTURE -Crystalline constituents of a prepared surface observed through a microscope with magnification usually at 100x and higher.
MODULES OF ELASTICITY – A measure of the rigidity of metal, including ratio of stress, below the proportional limit, to corresponding strain. Specifically, the modulus obtained in tension or compression is Young’s modulus, (also called stretch modulus or modulus of extensibilty). The modulus obtained in torsion or shear is modulus or rigidity, shear modulus or modulus torsion; the modulus covering the ratio of the mean normal stress to the change in volume per unit volume is the bulk modulus.
NORMALIZING – Common heat treatment for metals similar to annealing but does not appreciably soften the metal. Process done through heating a ferrous alloy above the transformation range, followed by air cooling to a temperature substantially below this range. Normalizing is typically used to restore uniform grain structure and relieve internal stresses caused by cold working.
OPEN HEARTH FURNACE – A type of furnace where excess carbon and other impurities are burnt out of pig iron, or cast iron used for remelting to produce steel. The open hearth furnace was developed to overcome the difficulty in manufacturing steel due to its high melting point. It is a reverberatory (repeatedly reflected heat) furnace. This is due to the shallow hearth and low roof which allows the material to be heated both by direct flame and radiation from the roof and sidewalls of the furnace.
OVERAGING – Term used to define the process of aging a material at a time and temperature greater than those required to obtain maximum change in a certain property. As a result, the properties of the material are altered back into the direction of its original state.
OVERHEATING – Process of heating a metal or alloy to such a high temperature that its original properties are impaired beyond restoration. Also known as "burning".
OXYGEN-FREE COPPER – Electrolytic copper free from cuprous oxide. Produced without the use of residial metallic or metalloid deoxidizers.
PASSIVATION – Treatment of a metal surface to reduce corrosion effects achieved through the process of changing a chemically active surface of a metal to a much more reactive state.
PENETRANT INSPECTION – A nondestructive test that locates discontinuities, which are open to the surface of a metal by first allowing a penetrtaing dye or fluorescent liquid to infiltrate the discontinuity thus removing the excess penetrate and then applying a developing agent that causes the penetrate to seep back out of the discontinuity and reveal the imperfection.
PHYSICAL PROPERTIES – Properties of a metal or alloy that are relatively insensitive to structure and can be measured without the application of force. For example, density, electrical conductivity, heat conductivity, and thermal expansion.
PICKLING – Removing surface oxides from metals by chemical or electrochemical reaction.
QUENCHING – Rapid cooling of a heated metal generally by immersion in liquid, to increase strength and hardness. Quenching is always followed by a temper to increase ductility.
QUENCH HARDENING – The hardening of a ferrous alloy by quenching from a temperature above the transformation range. This quenching takes place so that some or all of the austenite transforms to martsenite.
REDUCTION OF AREA – Measure of the ductility of metals obtained in a tensile test. This measurement, expressed as a percentage, is the difference between the original cross section of an area as opposed to the area of its smallest cross section after testing.
ROUGH MACHINING – A machining operation which allows ectra stock, usually to be followed by sunsequent operation, to be produced to accurate dimensions and finishes.
SCALING – The formation, at high temperatures, of thick oxidation product layers on a metal’s surface.
SHEAR STRENGTH – The stress required to produce fracture in the plane of a cross section. The conditions of loading must be such that the direction of force and resistance are parallel and opposite although their paths are offset by a specified minimum amount.
SOLUTION HEAT TREATMENT – Heating an alloy to a suitable temperature and holding it at that temperature long enough to cause one or more constituents to enter into a solid solution, and then cooling rapidly to hold these constituents in solution.
STEEL – A metal alloy whose major component is iron, with carbon being the primary alloying material. In steel, carbon acts as a hardening agent preventing iron atoms, which are naturally arranged in a lattice formation, from sliding past one another. Varying the amount of carbon and its distribution in the alloy controls the qualities of the resulting steel. Steel with increased carbon content can be made harder and stronger than iron, but is also more brittle.
STRAIN – Measurement of the deformation of materials caused by stress, or relative change in the size or shape of a body.
a) Linear Strain – the change per unit length of a linear dimension. Typically when the term "strain" is used alone, it usually refers to the linear strain in the direction of applied stress.
b) True Strain – (or natural strain) is the natural logarithm of the ratio of the length at the moment of observation to the original gage length.
c) Conventional Strain – the linear strain over the original gage length.
d) Shearing Strain – (or shear strain) is the change in angle, expressed in radians, between two lines originally at right angles.
STRESS – Internal forces, produced by application of external load in order to produce strain or pressure on an object, tending to displace component parts of the stressed material. Stress is measured in units of force per area, or the amount of force exerted in an object.
a) Normal Stress – normal and parallel to the plane.
b) True Stress – force and area are measured at the same time.
c) Conventional Stress – applied to tension and compression test, force divided by original area.
d) Nominal Stress – computed by simple elasticity formulas, ignoring stress raisers and disregarding plastic flow.
STRESS-CORROSION CRACKING – Failure of an object by cracking under combined action of corrosion and stress, either external (applied) or internal (residual). Cracking may be either intergranular or transgranular, depending on metal and corrosive medium.
STRESS RELIEVING – Process of reducing residual stresses in a material by heating it to a suitable temperature and holding it there for a sufficient time, and later cooling ti slowly in order to minimize the development of residual stresses. This treatment may be applied to relieve stresses by casting, quenching, normalizing, machining, cold working or welding.
STRESS RUPTURE TEST – A tension test performed at a constant temperature where the object is stressed under a constant load until it breaks. Data recorded commonly include: initial stress, time to rupture, initial extension, creep extension, and reduction of area at fracture (also known as "creep-rupture test").
SUPERALLOY – A "high performance alloy" developed for high temperature service characteristics including superior mechanical strength, good surface stability, and corrosion resistance; can withstand high temperature without oxidizing or losing mechanical properties. Typical applications include the aerospace industry, where superalloys may be in turbines, blades and jet engines.
TEMPER/TEMPERING – In heat treatment, to reheat hardened steel or cast iron to a temperature below the eutectoid temperature (or reversible reaction temperature when a solid solution in the cooling process is converted into two or more intimately fixed solids) to achieve a balance between strength and brittleness. Tempering a material after quenching or normalizing decreases hardness and increases toughness.
TENSILE STRENGTH – In tensile testing, the ratio of maximum load to original cross sectional area. Measured in psi (or pounds per square inch) through a tensile test conducted by longitudinally stretching a material at both ends until it reaches its breaking point and is forcibly pulled apart. The load required to break the material is the ability of the material to withstand tension up to that point. The higher the psi (breaking strength), the stronger the material.
TORSION – A twisting action resulting in shear stresses and strains.
TOUGHNESS – Measurement of a materials ability to absorb energy or deformation without breaking created by bending, impact, etc. High toughness requires both high strength and high ductility.
TREPANNING – Type of boring that includes creating an inner diameter into a solid piece making a leftover core.
ULTIMATE STRENGTH – The maximum conventional stress (tensile, compressive or shear) that a material can withstand prior to failure or rupture.
ULTRASONIC WAVES – Waves of ultrasonic frequency, which include longitudinal, transverse, surface and standing waves. Steel and other forms of materials can be "ultrasonic tested" to detect any impurities within the object that can’t be seen by the naked eye.
VACUUM MELTING – Melting that takes place under reduced pressure ranging from sub atmospheric pressure to ultra-high vacuum. This type of melting is used to prevent contamination from air, and to remove gases already dissolved in the metal; the solidification may also be carried out in a vacuum or at low pressure.
WORK HARDNESS – Hardness developed in metal as a result of hard working.
YIELD POINT – Only certain metals express yield points, which are the first sign of stress in a material, usually less than the maximum attainable stress, at which an increase in strain occurs without an increase in stress. Basically, the point where the material becomes permanently distorted.
YIELD STRENGTH – The stress at which a material exhibits a specified deviation from proportionality of stress and strain. An offset of .2% is used for many fields.